Challenge
Cauli Ltd approached Unifabs about their packaging collection kiosk manufacture requirements. These collection kiosks form an integral part of their pioneering Cauli Reuse System (CauliRS), CauliBox food and drink packaging reuse system. It was vital that they were manufactured to a high specification and within budget. Situated in workplace canteens, universities, and hospitals in the UK, the kiosks needed to be durable with a high quality of finish to withstand repeated use by the public. It was also important to the client that they found a reliable and cost-effective supplier. One that they could build a long-term partnership with.
Solution
Upon receiving designs, Unifabs’ engineering design team reviewed the kiosks with manufacturability in mind. Over time they manufactured small batches of kiosks, working in close collaboration with the client’s engineering team to ensure the integrity of the product.
Along with the client’s engineering team, some adjustments to the design were identified to enable kiosk manufacture to be efficient, cost effective and repeatable. Taking proven learnings from an established product that we manufacture for a different industry, we made changes to the design of the kiosk’s door to improve functionality and durability, ensuring longevity in use.
We also made some adjustments to the side panels, increasing from two to four, to enable them to be much simpler to fold, powder coat and assemble without affecting the product’s aesthetics. Moreover, this adjustment added strength to the product while reducing costs.
We identified further opportunities to eliminate costs in the forming process. Specifically, by using step folding to achieve a large radius, we eliminated the need for expensive tooling while maintaining the aesthetics of the end product.
Result
Several batches of Cauli collection kiosks have been manufactured and delivered in the UK. These were within the client’s budget, whilst maintaining the required quality expectations.
Close collaboration with the client’s design team and continuous improvements have enabled more efficient manufacturing and assembly of the product. By making some minor amendments to the design, the components could better suit the automated capabilities within our production, leading to cost savings for the client. The result is a stronger product which is more durable and easier to assemble.
With a mission to save 15,000,000 single-use takeaway containers every year, we are excited to continue working with Cauli as they grow to achieve their vision.
Team Feedback
We are delighted to be entrusted with creating Cauli’s collection kiosk. It is a perfect example of how close collaboration and continuous improvements can benefit an end product in terms of manufacturability, functionality, cost and quality.
Sales Account Manager
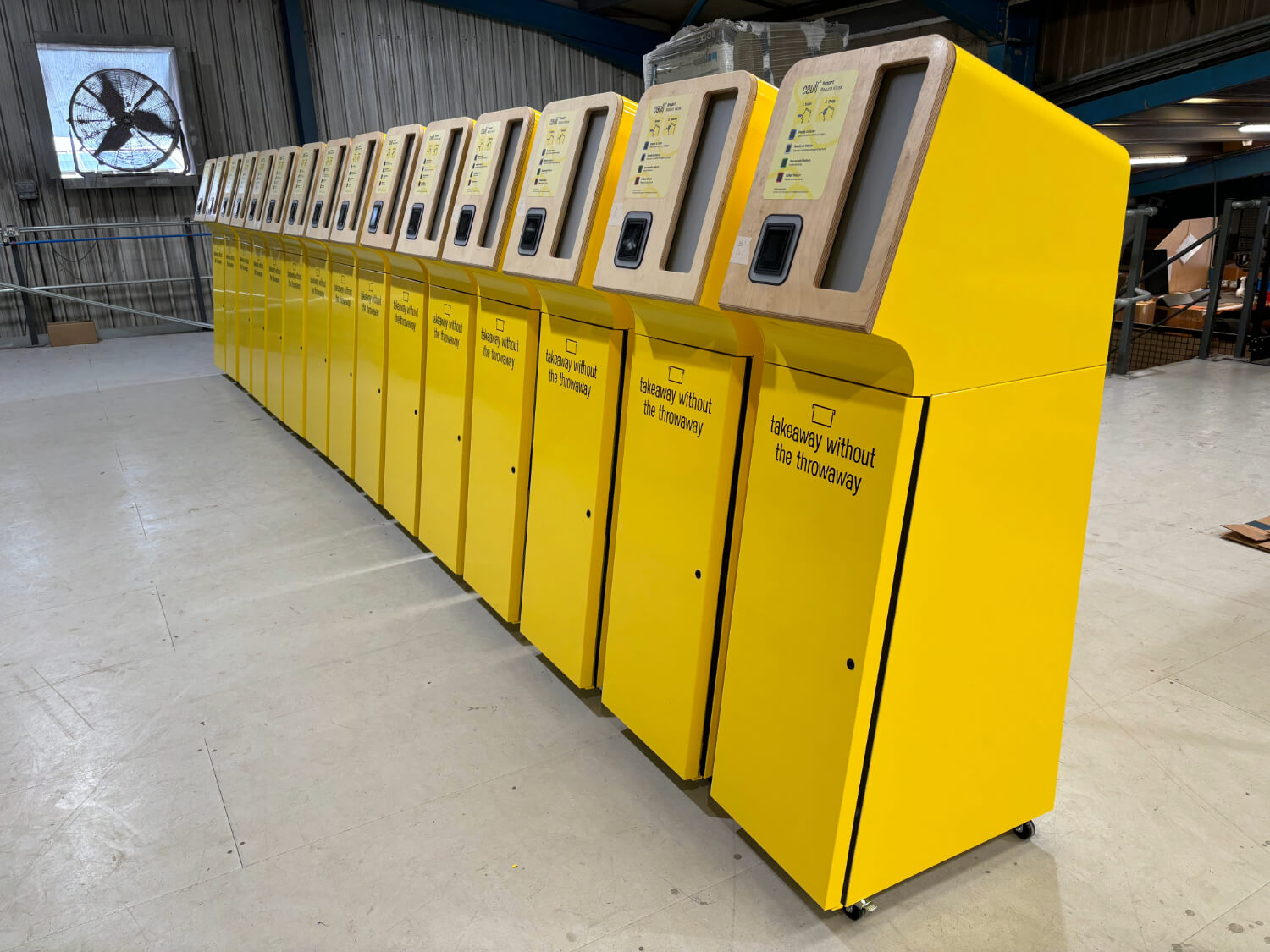