Introduction
Sheet metal is one of the most commonly used materials in manufacturing. The properties of sheet metal, such as its malleability, hardness and durability make it ideal for many applications.
Sheet metal can be used to manufacture a wide range of products including automotive components, appliances and packaging. Sheet metal is also an efficient material because it requires less energy than other materials such as plastic or wood. However, despite its many benefits, there’s always room for cost reduction in sheet metal manufacturing when producing parts yourself or working with a supplier.
At Unifabs, we understand the pressures our customers face to reduce costs without compromising on quality. As a trusted sheet metal manufacturer, we’ve worked with various industries to help optimise designs, streamline processes, and cut costs. Here’s how you can save money on your sheet metal parts while maintaining performance and reliability.
In-house production: Is it always cost-effective?
In-house production can indeed be a cost-effective solution, but it’s important to evaluate whether it aligns with your resources and expertise. If you’re not sure whether in-house production is right for you, here are some key questions to consider:
Is the part simple to produce?
Yes:
If the part is straightforward and doesn’t require complex processes or specialised equipment, in-house production can be feasible.
No:
Complex parts might require expertise and machinery that you don’t have, making outsourcing a better option.
Do you have the necessary expertise?
Yes:
If you or your team possess the necessary skills and knowledge, producing the part in-house can save costs and offer more control over quality and timelines.
No:
Lacking the expertise could lead to production issues, increased costs, and lower quality.
Is volume high enough to justify in-house production?
Yes:
Large production runs can spread out equipment and labour costs, making in-house manufacturing more viable.
No:
For smaller production runs, the costs of setting up in-house production may outweigh the benefits, and outsourcing might be more cost-effective.
If you find that in-house production isn’t right for you, outsourcing to a partner like Unifabs can bring both cost and operational advantages.
Leverage automation for cost efficiency
Automation is the use of machines to perform work that would otherwise be done by people. Automation can reduce the cost of production by increasing efficiency and reducing the need for human labour. Automation can also increase quality and consistency.
At Unifabs, we invest in advanced technologies like automated panel bending and laser cutting, which reduce human error, improve precision, and shorten production times.
Automating your production line with a partner who has state-of-the-art equipment can significantly lower costs, especially for large volumes.
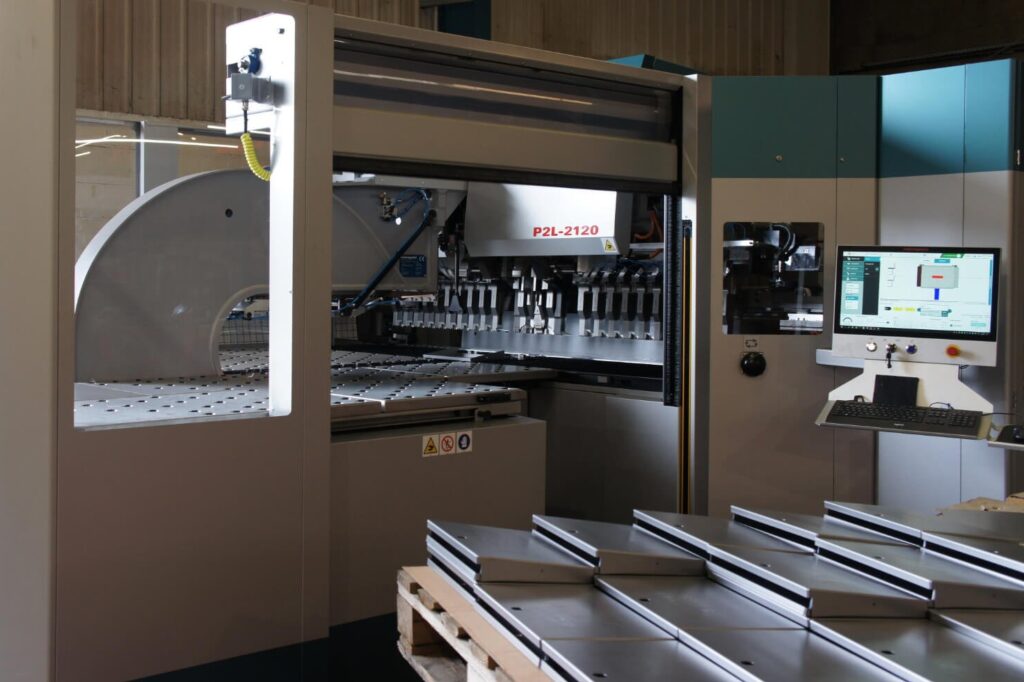
Material selection
Choosing the right material is key to balancing cost savings and product performance. Opting for less expensive materials can significantly reduce the cost of your manufactured parts, but it’s important to consider factors like durability and recyclability when making your selection. For example, using a thinner gauge of sheet metal, such as 2mm instead of 3mm, can reduce costs as long as it still meets the necessary structural requirements.
While cheaper materials, like plastic, might seem like the obvious choice over steel for certain applications, long-term considerations such as maintenance and disposal are crucial. In some cases, steel—despite its higher upfront costs—may be the better option due to its durability and ease of maintenance.
At Unifabs, we’ve helped clients in industries like agriculture cut costs by transitioning to more efficient materials. For instance, we assisted a client in switching from a costly composite to a steel alternative that was more durable and cost-effective. You can read more about how we achieved this in our case study here.
Standardisation for greater efficiency
Standardisation of products can also lead to significant cost reduction in sheet metal manufacturing.
Standardising parts and designs can reduce costs by minimising tooling changes, simplifying production, and improving quality control. By reducing the variety of parts and processes needed, you also lower training requirements, reduce documentation needs, and streamline inventory management.
Understanding Minimum Order Quantities (MOQ)
MOQ can greatly affect the cost of your parts. Higher volumes typically reduce the per-unit cost because manufacturers can spread setup costs over more parts. Understanding the balance between MOQ and unit cost can help you negotiate better deals and save on production. At Unifabs, we work with our clients to find the right balance between quantity and cost, ensuring competitive pricing for both small and large orders.
Optimising design for cost reduction
Design is a powerful tool when it comes to cost reduction in sheet metal manufacturing.
By focusing on design for manufacture and incorporating value engineering exercises, businesses can generate or unlock significant savings. At Unifabs our design team excels in these processes, helping customers develop products that are both high-quality and cost-effective. Simple changes allow for designs to be optimised for production in a certain way, like eliminating unnecessary welds through innovative panel bending techniques.
Collaboration early in the design phase allows for optimisation of designs for manufacturing processes, driving down costs, minimising waste, and reducing lead times while elevating quality, and ensuring products are crafted with care and expertise.
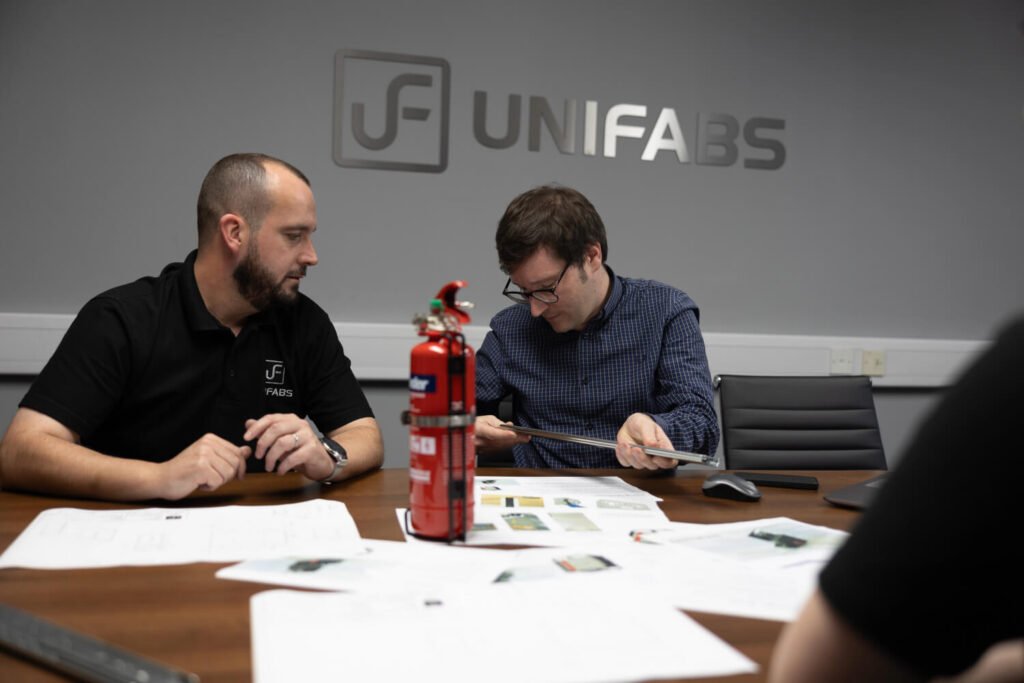
Choosing the right manufacturing partner
Your supplier is a crucial partner in ensuring the success of your project.
When selecting a manufacturing partner, prioritise those who not only deliver on time but also bring innovation and problem-solving to the table. Look for companies that are responsive, reliable, and have a track record of consistently meeting high-quality standards.
At Unifabs, we excel in providing tailored design solutions that enhance product quality, improve efficiency, and drive overall performance, ensuring that your projects are delivered with precision and care.
Conclusion
We hope that this article has given you some insight into how to save money on sheet metal manufacture.
Cost savings don’t have to come at the expense of quality. By making strategic choices in materials, design, and production processes, you can reduce costs while still delivering exceptional products.
Unifabs is here to help you every step of the way—whether through design consultation, material selection, or full-scale production. Contact us today to learn more about how we can help reduce your costs without compromising on quality.