As the industry becomes increasingly competitive, manufacturing companies must find ways to improve their production capabilities. Unifabs Limited, a UK-based sheet metal manufacturing and design company, has invested in a second Salvagnini P2 automated panel bending machine. Increasing its production capacity to meet the growing demand for its services.
The Salvagnini P2, installed in July 2023, joins another Salvagnini P2 alongside an extensive range of traditional press brakes at the company’s forming facility in Galley Common, Nuneaton. The decision to invest in a second machine was made to increase the company’s production capacity. It will also reduce lead times for its customers following a significant increase in demand for bending services. This addition represents a doubling of capacity. Thus, aims to offer Unifabs’ customers a faster turnaround time without compromising on the quality of its products.
Benefits of automated panel bending
This panel bending machine offers several benefits for Unifabs and its customers. Not only is there the increase in capacity for bending services, enabling the business to take on more contracts and meet the growing demand for its services. It also means that the company can take on larger orders. Thus providing it with competitive advantage over other sheet metal manufacturing companies.
In addition to this, having a second Salvagnini P2 can act to alleviate any potential scheduled, or unscheduled downtime on the other machine. For instance routine maintenance can now be better managed to cause minimal impact on contracts.
The new machine also brings increased efficiency to Unifabs’ production process. This highly automated machine can bend sheet metal to form parts quickly and accurately with minimal human intervention. Thus reducing the need for skilled manual labour as is required by a traditional press brake. Some of its integrated features such as its ability to bend in both directions, speeds up the production process as it eliminates the need to manually manipulate the sheet in between folds.
Unifabs’ technical design department has also realised potential benefits for its customers through the use of the Salvagnini P2. Its capabilities unlock design and commercial improvements, creating possibilities to combine multiple parts into a fully folded piece removing the requirement for welding or riveting. Removal of additional processes reduces costs and time to manufacture, and can improve a product’s aesthetics. The second machine will provide capacity for even more products to benefit.
Salvagnini P2 automated panel bender features and capabilities
With its advanced technology, precision, and flexibility, the Salvagnini P2 is an invaluable addition to a production line. What makes it stand out from traditional panel bending machines is its ability to perform a variety of different operations with minimal human intervention. Thus allowing manufacturers to scale their operations and stay ahead of their competition in an ever-evolving industry.
The P2 utilises universal bending tools which automatically adapt without machine downtime. This, coupled with its integrated adaptive technologies which enable the machine to automatically adapt to changes in the material, mean a flexible and adaptive system delivering accurate and repeatable results.
Advantages of automation in sheet metal fabrication
Automation in fabrication not only reduces lead times but also increases overall productivity, efficiency and improved safety. Automated processes such as robotic welding, automated panel bending and material handling and storage systems, can provide many advantages in manufacturing. Automation typically allows for greater precision and accuracy. It minimises the likelihood of errors, and also ensures that each product meets the same high standards. As a result not only can manufacturers produce more products in less time, but they can also do so with greater consistency and reliability. This creates a competitive advantage in the market and helps to drive growth for businesses that adopt this technology.
Machines utilising CNC (computerised numerical control) technology have revolutionised the manufacturing industry. This technology enhances the speed and accuracy of sheet metal production. Couple this with automation in sheet metal feeding and storage systems, such as those used with the laser profiling systems at Unifabs, and machines are able to work non-stop, consequently minimising downtime and maximising output.
Unifabs’ commitment to quality
Unifabs is committed to delivering high-quality products and exceptional customer service. Their investment in a second Salvagnini P2 bending machine is just one example of their commitment to maintaining state-of-the-art production capabilities and meeting the growing demand for their services.
Read more about the Salvagnini P2 and the automated panel bending services offered by Unifabs Limited.
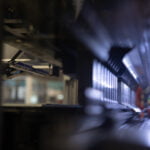
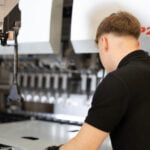
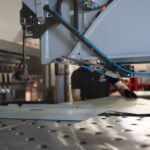
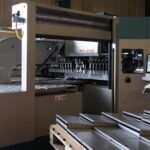