Introduction
As the smart locker sector continues to evolve, driven by the rise of e-commerce, contactless deliveries, and secure click-and-collect services one thing remains clear: high-quality, scalable sheet metal fabrication is essential to bringing these innovations to life.
Why Sheet Metal Fabrication Matters in Locker Manufacturing
Smart lockers are no longer just simple storage units. They’re connected, intelligent systems that need to be strong, secure, clean, and easy to customise and brand. These requirements place significant demands on the structural enclosures that house them—where high-quality sheet metal fabrication becomes essential. Precision-made sheet metal components, produced through carefully controlled fabrication processes, are vital in ensuring these systems perform reliably in the most demanding environments.
Whether located outdoors in public spaces or within retail, logistics or residential areas, smart lockers must be tough and built to last. This is where expert locker manufacturing, supported by advanced sheet metal fabrication, makes a difference. Offering structural strength, design flexibility and a high-quality finish.
At Unifabs, we support smart locker manufacturers across a broad range of UK applications, from parcel collection and click-and-collect lockers to specialised systems such as secure electronic key cabinets. Our expertise covers fully assembled kiosk enclosures, precision-formed internal panels, and high-security housings designed for integrated access control. We help clients meet tight tolerances, fast lead times and the practical demands of busy public spaces and secure sites alike.
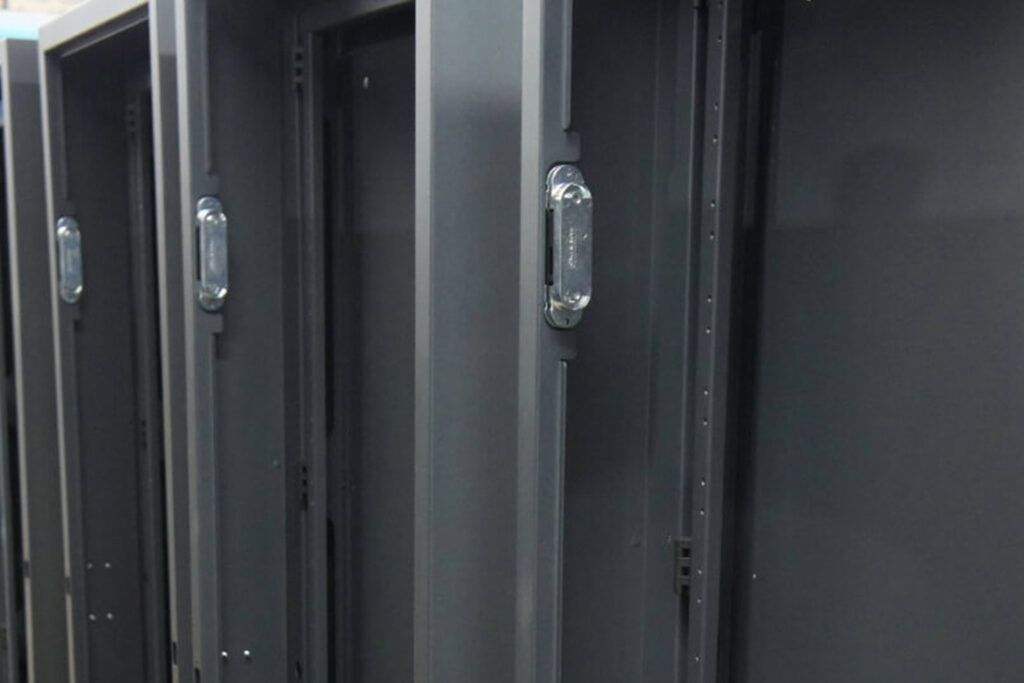
Durability and Structural Integrity
Smart lockers are often installed in environments where reliability is critical. Exposed to repeated use, outdoor conditions and the risk of tampering, strong metal enclosures are central to ensuring performance.
Commonly used materials include mild steel, stainless steel and aluminium. Each offers different advantages depending on environmental and design requirements. Fabrication techniques such as MIG and TIG welding help build strong, long-lasting frames, while robotic welding ensures consistency and speed at scale.
For example, when fabricating outdoor units for logistics customers, we’ve used pre-galvanised steel with added powder coating to protect against corrosion in all-weather conditions, ensuring structural integrity and a long product lifespan.
Surface Finishing for Function and Aesthetics
In public-facing and high-traffic areas, the finish of a smart locker isn’t just about looks, it’s also about durability. Powder coating is a popular choice in locker manufacturing. It offers protection against rust, wear and even graffiti. Smooth powder-coated finishes are easier to clean and maintain, which is particularly important in food service, healthcare and busy retail environments.
We’ve worked with retail and food service clients to supply lockers in clean, high-touch finishes in custom RAL colours. These not only enhance visual appeal but also support hygiene and ease of upkeep.
Finishes may also need to support branding elements, signage, or user interaction zones, so they must hold up well under daily use.
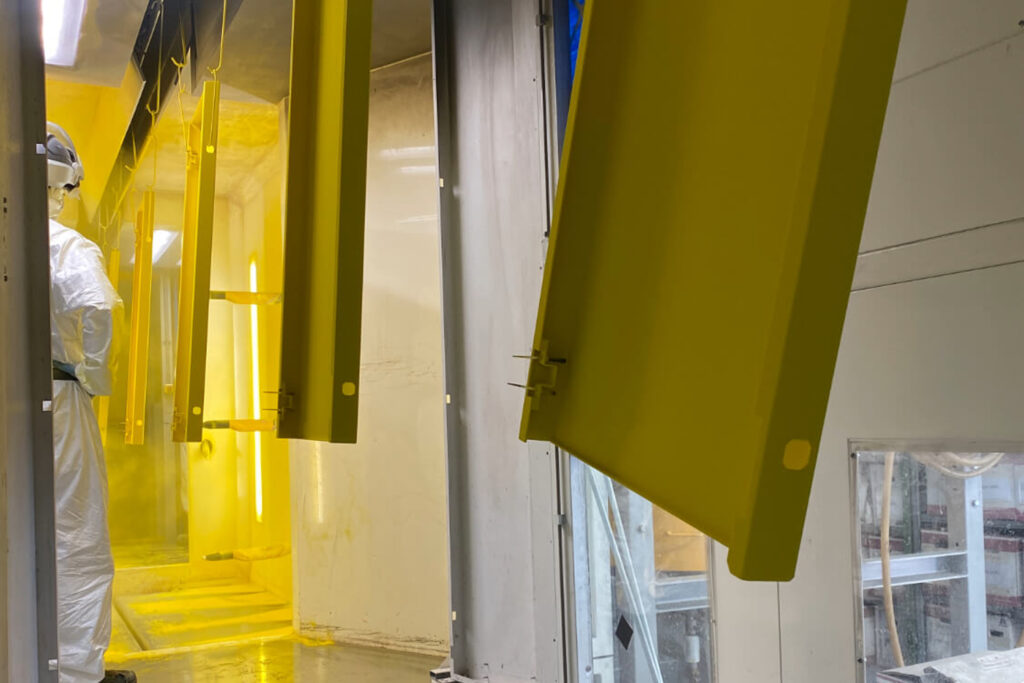
Designed for Technology and Access
Modern smart lockers include a range of integrated technologies: touchscreens, barcode or QR scanners, RFID readers and wireless modules. The sheet metal enclosure must be designed to accommodate these components without compromising protection, ventilation or usability.
Design for Manufacture (DFM) is essential. Using CAD models, fabricators can plan for cable routing, mounting points, cooling vents and service access, ensuring that everything fits.
Our in-house design team regularly collaborates with customers on prototypes requiring integrated access panels, touchscreen cut-outs and ventilation zones. All of these are CNC-machined to exact specifications using our CAD-to-production workflow.
Design automation tools also support rapid iteration, making custom locker manufacturing more efficient and repeatable.
Scalable Production, Repeatable Results
As smart locker demand grows, manufacturers need to move from prototype to full production quickly and efficiently. Modern sheet metal fabrication allows for repeatable precision across hundreds or thousands of units, supported by automated cutting, folding, welding and finishing systems.
Thanks to our investment in high-end machinery, Unifabs can deliver this repeatability at scale, ensuring quality, consistency, and performance whether producing 10 units or 1,000. This scalability is vital not only for meeting tight lead times but also for maintaining standards across large, multi-site deployments.
Beyond the Enclosure: Practical Considerations
The visible outer frame is just one part of a smart locker. Behind the scenes, effective sheet metal design also considers internal layout and features, including airflow (both passive and active ventilation), weatherproofing to meet IP ratings, internal brackets and component mounting, and cable management.
Other requirements, such as DDA compliance, fire resistance or anti-tamper features, can vary depending on the market. This is where flexibility in materials, fabrication techniques and assembly methods becomes essential.
Conclusion
As smart lockers become a more familiar part of daily life, handling everything from parcel delivery to secure storage in retail and residential spaces, their physical design must keep up with growing expectations. Sheet metal fabrication is central to that evolution, ensuring lockers are built to perform, look professional, and last.
Our work with companies like e‑Track, who produce secure electronic key cabinets, showcases how precision fabrication supports even the most sensitive smart locker applications—where security, reliability and integration are non-negotiable.
As a trusted fabrication partner to locker manufacturers across the UK, Unifabs helps bring new concepts to life faster—with the scalability and consistency needed for large-scale deployment.

Optimised designs help products thrive
Contact us today to discuss our design for manufacture process and your design requirements.