A leading agricultural machinery manufacturer, McConnel Ltd, wanted to source a cost effective and durable solution for the rear casing on one of their market leading remote controlled mower systems. The original casing was made from a composite material. Due to supply and performance issues, they were looking to source an alternative solution. Unifabs were provided with a drawing of a steel fabricated alternative to the part for review to ensure it could be optimally fabricated utilising its range of manufacturing capabilities.
Due to the complexity of the shape and volume of weld and linish required, the manufacturing method would need to be altered to ensure a consistent product, similar in finish and appearance to the composite material.
Supporting customers through Design for Manufacture service
Unifabs experienced in-house manufacturing design team reviewed the designs. After close consultation with the customer, we altered the makeup of the part to allow for it to be manufactured in a cost-effective and repeatable manner.
The complex part, designed out of multiple sheet metal components, required two operators to fold and form the product. Following the design review we were able to remove this requirement, reducing it to just one operator. Due to the complex nature of folding required, break-off tabs were added to aid the operator and speed up folding.
To further speed-up the process and achieve repeatable consistency, we designed two jigs for integration with our robot welder. These acted as both a welding fixture, to hold the part in place, and a checking fixture for tolerance. The design team created two programmes offline in 3D, one for each side of the part, allowing for the part to be fully welded on the robot welder. This enabled repeatable consistency and precision to the welds. The casing was then linished to create a smooth continuous finish. Fixtures were then reused to ensure everything was in tolerance.
Design benefits from prototyping
A prototype was produced for the customer. Following this, we saw an additional opportunity to remove a visible weld by further changing the folding. A second sample was produced which ultimately improved the appearance of the product for the customer. As a result Unifabs were able to successfully replicate the composite product in a cost-effective manner producing a much more durable casing, and ultimately enhancing the end-product. This design for manufacture service led to several orders with the view to regular repeats in the near future.
Could design services help you?
Maybe you have similar issues with materials. Or perhaps you have a product which is long overdue a redesign to make it more easily and cost-effectively manufactured. Maybe we can help. Find out more about how we support our customers through our manufacturing services, or contact us to discuss your requirements.
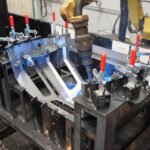
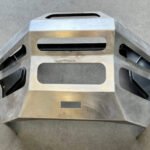
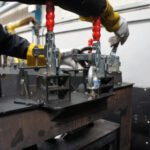
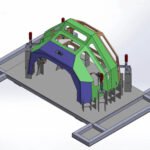
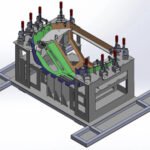
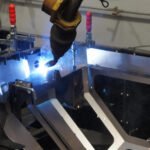