Press-braking and panel bending are pivotal processes in the sheet metal industry, each offering unique advantages and disadvantages. Investing in new equipment for sheet metal manufacturing can be costly. You need to carefully consider the business’s specific requirements and constraints when choosing what sheet metal bending methods to invest in.
Unifabs recently invested in a further Salvagnini automated panel bending machine. Today we thought we’d share with you some of the pros and cons of these methods. Things to consider as a manufacturer when investing in new bending equipment. And, also to give an insight into some of the reasons why we might choose one method over the other when producing a product.
Sheet metal bending methods – Panel bending vs press brake, pros and cons outlined
Press-Braking Pros and Cons
Pros
- Versatility: Press-braking is highly versatile and can be used for a wide range of sheet metal bending applications.
- Cost-Effective: Press-brakes tend to be more affordable upfront, making them an attractive option for smaller manufacturing operations.
- Compatibility: Press-brakes are compatible with a wide variety of sheet metal materials and tooling.
Cons
- Slow Production: Press-braking is often slower than Salvagnini panel bending due to manual tool changing and setup times, which can be a limitation for high-volume production.
- Manual Labour: Requires manual labour for set-up and loading and unloading sheets with multiple people required for larger parts which may lead to operator fatigue.
- Operator Skill: Higher operator skill is required, often achieved over many years due to the large variation of tooling and processes to familiarise with.



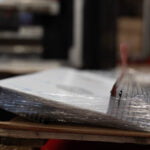

Salvagnini Panel Bending Pros and Cons
Pros
- High Speed: Salvagnini panel bending is known for its high-speed production, making it ideal for large quantities.
- Automation: Offers high levels of automation, reducing the need for manual labour and ensuring consistent quality.
- Operator Skill: Offline programming at the design stage often means the operator only needs to make minor angle corrections on a new part reaching the machine.
- Complex Shapes: Capable of creating complex and intricate shapes with high precision.
- Reduced Tooling Costs: The machines have a universal set of tooling that is purchased once within the cost of the machine.
Cons
- Higher Initial Cost: The machinery and automation systems for Salvagnini panel bending are typically more expensive, which can be a barrier for smaller businesses.
- Material Thickness Limitations: The Salvagnini's at Unifabs can process up to 3mm thickness however depending on the angle required, this may be less.
- Size Limitations: The overall length of parts is limited to the machine bed. It is also limited on small sizes due to the fixed tooling.
Conclusion
Both press-braking and Salvagnini panel bending offer distinct advantages and disadvantages. The choice between the two methods largely depends on the specific needs, budget, and production scale of the manufacturer. Smaller operations with varied material requirements and limited budgets may find press-braking more suitable. While large-scale manufacturers aiming for high-speed, automated, and highly precise production may favour Salvagnini panel bending. We are in a great position to have been able to heavily invest in both types of machinery.
Recommendations to others
Manufacturers should consider the following factors when deciding between press-braking and Salvagnini panel bending:
- Production volume
- Budget constraints
- Material requirements
- Level of precision and complexity
- Operator expertise
- Long-term maintenance and operational costs
By carefully assessing these factors, manufacturers can make informed decisions on which sheet metal bending methods to invest in. Ones that align with their production goals and business objectives. Contact us today to discuss your metal bending requirements and let us help your component or project take shape.